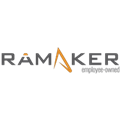
Ramaker & Associates, Inc.
Sauk City, WI 53583
Making Energy Conservation a Part of Your Facility
Through its most basic definition, energy conservation refers to efforts made to reduce energy consumption. This can be achieved through increased efficient energy use, in conjunction with decreased energy consumption, and/or reduced consumption from conventional energy sources. Energy conservation can result in increased financial capital, environmental quality, and guest comfort. Owners/operators can choose to conserve energy in order to reduce energy costs, increase efficiency, and maximize profit.
The energy costs associated with operating an indoor waterpark are second only to the cost of the staff necessary to manage it. The staff requirements can vary somewhat depending upon the attraction, but many owner/operators are looking for opportunities to reduce energy costs to improve the profitability of their facility. In this article, we will discuss what is being done today to control energy consumption and still maintain healthy indoor air quality (IAQ).
While it is acknowledged that architectural design of a facility plays a big role in energy use, this article focuses mainly on the mechanical and electrical systems associated with waterparks. We will share with you the newer technologies out there; what is being done today versus 10-15 years ago; and some of the available options with all the details – good, bad or indifferent.
HVAC Considerations
Selecting the correct HVAC system for your facility is critical to minimizing operating costs. A large waterpark could use 100,000 or more therms (one therm is approximately the energy equivalent of burning 100 cubic feet of natural gas) of heating energy per year. To follow are several of the common systems used today with the associated advantages and disadvantages.
An energy recovery ventilator is a system where the supply air consists of 100 percent fresh outside air and the return air is exhausted with no recirculation. Typically, the supply and exhaust streams pass through a heat exchanger to recover sensible energy from the exhaust air, but the two streams are not directly mixed. Typical efficiency of the heat recovery section is around 60 percent. Some systems are available with enhanced control of the outside air percentage.
This system’s benefit is that the use of outside air exclusively allows for the best opportunity to control air contaminants and maintain IAQ. Also, this system can effectively control indoor humidity and temperature in moderate climates by replacing moist, stale air with fresh, drier outside air.
The disadvantage is that it is more energy intensive, particularly in colder climates because of the large outside air volume. Also it is not a suitable approach for humidity control/cooling in southern states where outside temperatures remain very warm and humid for extended periods.
A packaged system with mechanical dehumidification is very prevalent in smaller indoor pools, such as those found in hotels. The humidity in the pool area is controlled by mechanical refrigeration, and typically only the minimum amount of outside air is used. Supplemental heat is provided by electric or hot water/steam coil. Some energy can be recovered from the refrigeration process which is usually rejected into the pool water or air space.
An advantage to this system, if sized correctly, is it can do a good job of controlling indoor humidity. Additionally, modern systems incorporate heat pumps to increase overall efficiency and utilize dual refrigeration circuits. Furthermore it is usually the lowest first cost option, particularly for small recreational pools.
On the negative side, it provides minimal ventilation levels to reduce compressor requirements. Most of these units do not offer economizer cycles to provide the benefits of the 100 percent outside air systems. Additionally it requires operation of compressors or heat pumps to control humidity.
An exhaust only system is a lower cost supplement for a 100 percent outside air system. In this approach, high volume exhaust fans are used to move outside air through the facility. During warmer months, utilizing these fans in lieu of other air handling equipment can save significant energy since the exhaust fans operate at a lower pressure and require far less horsepower. In a normally warm climate, this approach could serve as a primary source of ventilation.
To illustrate the benefit of exhaust systems, a typical 30,000-square-foot waterpark may have an energy recovery ventilator that operates with four 30-horsepower fans. During the warmer months, the waterpark could be ventilated using three 20,000-cubic feet per minute (cfm) fans that operate with less than five horsepower each.
Many systems being installed today are hybrids of the types described above. The actual system your designer recommends will depend upon where the facility is located. Above is a map that indicates three general areas of consideration.
Zone 1 is temperate and covers most of the continental U.S. In this zone there is usually ample opportunity to utilize outside air to control humidity and temperature inside a waterpark. A typical system would incorporate an energy recovery ventilator with direct fired gas or hot water heating. The use of refrigeration systems to control temperature and humidity is not required. A supplemental exhaust system could be added to reduce energy consumption during warm weather. To further reduce energy consumption, the energy recovery ventilator can be equipped with advanced controls that monitor indoor humidity or space occupancy to vary the amount of outside air to match demand.
Zone 2 is the desert southwest where the temperatures can exceed 100°F routinely with very low relative humidity. In this zone many designers consider energy recovery ventilators that utilize evaporative cooling to control temperature, and also provide humidifiers to reduce evaporation and energy loss from the waterpark. The humidification process on this scale can be energy intensive, and is often accomplished by steam injection. To balance evaporative losses with humidification expense, the target humidity levels in the waterpark are often lowered below the typical 40 precent.
In Zone 3 the use of outside air to control humidity is limited since temperatures can get very warm with high humidity. Even the use of a high volume exhaust system will add little benefit. In this situation the designer will likely choose energy recover ventilators with a supplemental dehumidification system. Large waterpark facilities may also require a chiller plant to meet cooling demand.
Electrical Considerations
A prime item to look at for electrical energy efficiency in a waterpark is the motors. This can have a significant effect on your bottom line. You will want to determine whether the results provided by certain motors would be technologically feasible, economically justified, and offer significant energy savings.
A variable-frequency drive (VFD) is a system for controlling the rotational speed of an alternating current (AC) electric motor by controlling the frequency of the electrical power supplied to the motor. VFDs are widely used but only recently have they been incorporated into waterpark applications. In ventilation systems for large buildings, variable-frequency motors on fans save energy by allowing the volume of air moved to match the system demand. They are also used on pumps, elevator, conveyor, and machine tool drives.
The use of VFDs in commercial applications is not new, and is most commonly found in HVAC applications. Typically VFDs are integrated into air handling units and fans to allow precise speed control. Another benefit to the waterpark industry is the use of VFDs to control normally fixed speed pumps. In a typical waterpark there could be several hundred horsepower in pool recirculation and feature pumps. During the design phase, the engineer will size these pumps based on required flow rates and an estimate of the head loss through the system including a modest factor of safety. In some cases, local code dictates the minimum capacity for certain pumps.
Once the facility is built, the actual running conditions will vary depending upon how the contractor constructed the system. By using a VFD, the operator can fine-tune the pump to operate exactly where it needs to be. It is not uncommon to find VFDs on fixed speed pumps operating at 15 percent reduced speed, which by Affinity Law results in a drop in power consumption of nearly 40 percent. Typically, the payback time for VFDs on motors 15 horsepower or larger is less than a year, and many utilities will offer incentives for installing them on large commercial loads.
If the facility has existing motors that are not being controlled by VFDs, and consideration is being given to installing VFDs, then consult with an engineering firm or equipment manufacturer to provide the correct size VFD for the motor. If the motor is not rated for use with a VFD, then the efficiency gained by use of a VFD may be lost to shortened motor life and unwanted heat loss.
Lighting in a Waterpark
Traditional lighting design for indoor waterparks includes the use of 400- to 1,000-watt metal halide fixtures. Metal halide is an excellent light source, but it has some limitations. The lamps require warm-up time before they illuminate to full power. Once the lamps are at full light output, a loss of power can cause a delay of 5-10 minutes before the arc will re-strike. Metal halide fixtures are not suited for frequent on/off operation as this will drastically shorten the life of the lamp. Additionally, higher wattage metal halide lamps have notoriously short life spans. A typical 1000-watt metal halide will last less than 10,000 hours, resulting in more maintenance expense for the facility owner.
Over the past several years, LED technology and costs have improved, Manufacturers of LED light fixtures have retooled many of the assembly lines. Companies that made ballast for fluorescent light fixtures are making LED drivers and LED light boards. This has reduced the cost of LEDs to be very competitive and cost effective. In addition, the Illuminating Engineering Society put together guidelines for testing the quality of the light output, including measuring lumen maintenance and photometric measurements. Each LED has its own individual characteristics; no two are exactly alike. In the past, LED light fixtures manufactured side-by-side might have produced very different color renderings to the human eye. Nowadays utilizing LEDs of the same Standard Deviation Color Matching Step (sometimes known as the MacAdam ellipse), as well as a process known as binning, fixtures are able to attain a much more consistent light (color) output. Because the LEDs have a rated life of approximately 50,000 hours, LEDs have reduced the maintenance costs of facilities as compared to past light fixture sources.
Besides technology and cost, another benefit of using LED is controls. In the past, when using HID fixtures, there was a certain amount of time that had to pass before the fixtures were at full light output. This time varied from 5 minutes to 15 minutes depending on the technology used. Today, LED light fixtures are immediately on and off. One benefit of this immediate control is the use of LED light fixtures in the emergency egress lighting application, assuming the LED fixture is provided either with battery backup or an alternate power source. A second benefit is that many LED light fixtures have integral 0 to 10-volt dimming drivers. Some fixtures can even come with factory mounted networked control modules on the fixture. This combination of driver and control module allows for networked lighting control solutions which allows the facility to connect daylight sensors, occupancy sensors, manual controls, and time based controls to LED light fixtures. For example, if the waterpark has large walls with lots of daylight or roofs with lots of daylight, then fixtures can be either turned off or dimmed down to allow for appropriate levels of light with energy savings. Likewise, with each fixture or group of fixtures having integral dimming and controls, it is possible that one area of the waterpark will have enough daylight to be dimmed to minimum light output or even off, while another area of the waterpark may be under an opaque roof requiring full light output.
One of the future outlooks for LED lighting will be to use the networked controls cabling to provide data exchange. This internet-working of physical devices such as light fixtures, lighting controls, smartphones, buildings, and other electronics is also known as the “Internet of Things.” This added data exchange and communication within the facility is not only an energy saving strategy, for example lights can be turned off in rooms without occupancy, but also an excellent opportunity for preventative maintenance and replacing components before failure. In summary, the advancements in LED light fixtures is significant and continues to improve. While the fixtures continue to consume less power, the lighting controls of those fixtures provide even more energy savings.
Alternative Energy Sources
Heat pumps, in the simplest sense, are refrigeration units that have the ability to cool (air condition) or heat a space by transferring heat from one medium to another. Heat pumps are special air conditioners that can “reverse” the refrigeration cycle to generate heat when required. Although it may seem counterintuitive, it can be shown for most cases that it is more economical to move heat around than it is to create heat by burning fuels. Heat pumps are most efficient when there are areas in a facility that require simultaneous heating and cooling demand.
For larger multi-purpose facilities or resorts, there is public space that may require cooling for most of the year. By installing heat pumps in those areas, it is quite easy to collect the heat being generated from that cooling process and reject it in to another area, such as a waterpark. On a larger scale, the resort owner could consider running all the hotel rooms on water source heat pumps with a common condenser loop around the facility. This would allow the energy to be collected from the entire facility and utilized where it is needed. As an example, in a recent project a campus-wide condenser loop serving a 150-room hotel was designed to be able to provide up to 5,000,000 BTU/hr of waste heat to the attached waterpark.
Heat recovery chillers are generally used in institutional situations to meet large cooling demands. They function by refrigerating liquid down to 45° or so and distributing to cooling coils around a facility. The heat recovery chiller works backward and is often coupled with a geothermal loop to provide a source of heat energy.
With solar thermal technology, panels are installed outside to collect thermal energy from the sun by circulating fluid through the panels. This has the potential to produce significant energy but the payback needs to be looked at closely for each site. A recent thermal survey for a racing pool on the University of Wisconsin-Madison campus indicated the installed cost for a 2,000 square foot thermal solar system would be $90 per square foot and yield 5,400 therms annually. However, the simple payback period was 39 years. Solar thermal technology definitely can provide cost savings to facilities that use a lot of hot water. However, each site needs to be evaluated on a case by case basis to determine what is cost effective and if any incentive money is available.
Indoor Air Quality (IAQ)
We can reduce air handling equipment energy consumption if we monitor chloramines. We can increase or decrease the ventilation rates in response to an increase or decrease in chloramine levels. The better the water quality, the less ventilation required. Hence ultraviolet (UV) water treatment is often times installed to reduce the chloramine levels and improve water quality.
Building with long term interests into IAQ and other unseen, intangible features unconsciously attracts guests and improves profitability. IAQ cannot be seen, but it is definitely noticed by guests. Poor IAQ can cause stinging eyes from excessive chloramines or exacerbate asthmatic and other respiratory conditions. IAQ absolutely affects your business. If the guests don’t have a comfortable experience, they don’t come back. Great IAQ can be a key to success!
Conclusion
The relative merits of one design selection versus another will vary in many ways. The options considered here are not meant to be a completely comprehensive list of all energy savings alternatives. Selecting a system to achieve optimal energy efficiency takes time, research and, ideally, a long discussion with your design engineer. But with energy costs on the rise, the time and effort will be well spent when reduced utility requirements and operating expenses are realized.
About the Authors
Jeffrey Radue, P.E., the MEP Department Manager for Ramaker & Associates, Inc., has more than twenty five years of professional service within the consulting engineering industry. Radue has an extensive background in the design and analysis of HVAC, plumbing, power distribution, and lighting systems for industrial and commercial projects. His widespread experience in energy efficiency is a driving force behind offering the most current options to our clients.
Daryl Matzke, P.E., is a Vice President and the Director of the Aquatics Team at Ramaker & Associates, Inc. His specialty lies in managing large-scale, multi-discipline developments. With more than twenty six years of experience, he has led many successful waterpark development projects for clients nationwide.
Both can be reached by phone at 608-643-4100. For further information about Ramaker & Associates, Inc., please visit www.ramaker.com.